6月30日,我國最大液化天然氣儲備基地建成的消息在央視新聞頻道播出。
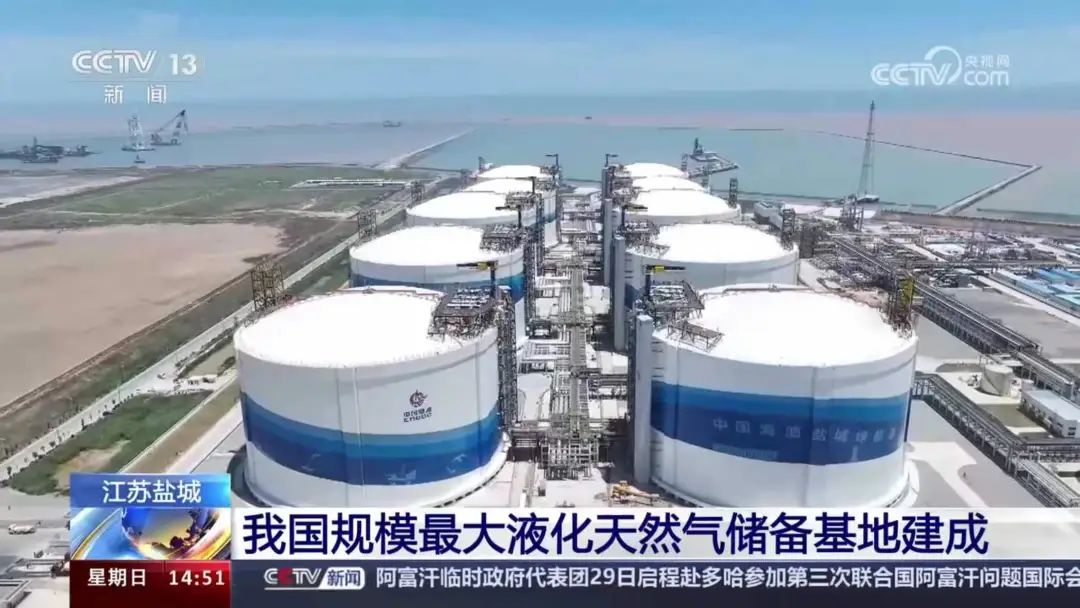
中國海油鹽城“綠能港”6座全球單罐容量最大的27萬立方米液化天然氣(LNG)儲罐在江蘇鹽城同步實現機械完工。
中海油石化工程有限公司(以下簡稱“海油石化工程”)江蘇濱海LNG一期擴建工程總承包項目組(以下簡稱“江蘇項目組”)洋溢著喜悅。
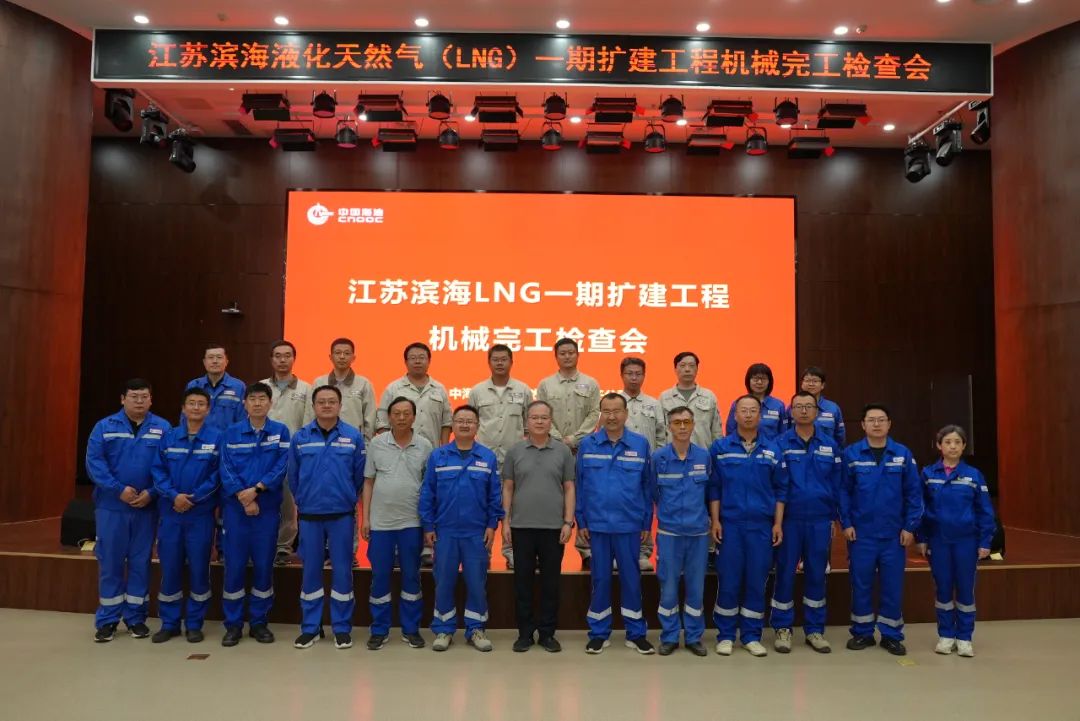
從2021年6月開工至今,海油石化工程作為總承包牽頭方,用三年時間將國內首批27萬立方米LNG儲罐群從藍圖變為現實,推進綠色能源超級工程自主設計建造技術國產化,LNG接收站總承包技術能力穩居國內第一梯隊。
“智”繪藍圖
因地制宜推進中國方案工程轉化
我國大力推進經濟社會綠色低碳轉型,天然氣作為清潔能源得到廣泛應用。中國海油按照國家天然氣產供儲銷體系建設要求,積極推進“綠能港”建設。“綠能港”意為綠色能源港,契合了LNG接收站的綠色能源保供使命。
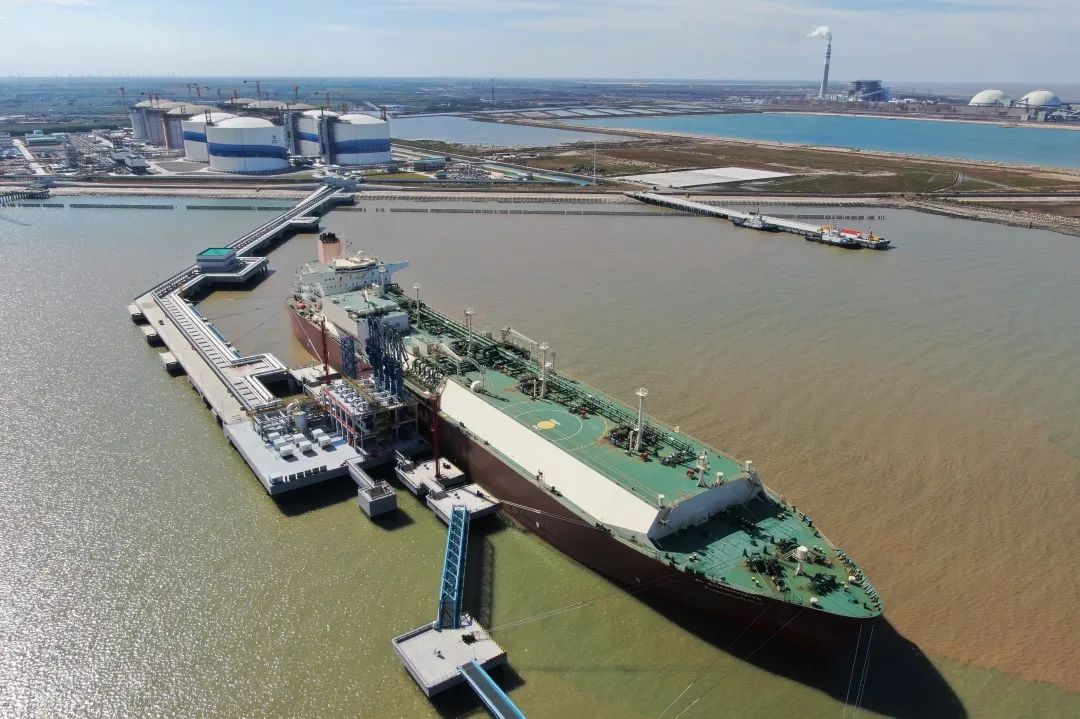
“海油石化工程積極參與‘綠能港’的設計和建造,”海油石化工程總經理吳廣增介紹說,“2007年以來,海油石化工程參與國內將近一半LNG接收站的技術咨詢、設計或建造,見證接收站儲罐規模實現從3萬立方米到16萬立方米、22萬立方米,再到27萬立方米的躍升,逐步掌握LNG接收站自主設計建造技術?!?/p>
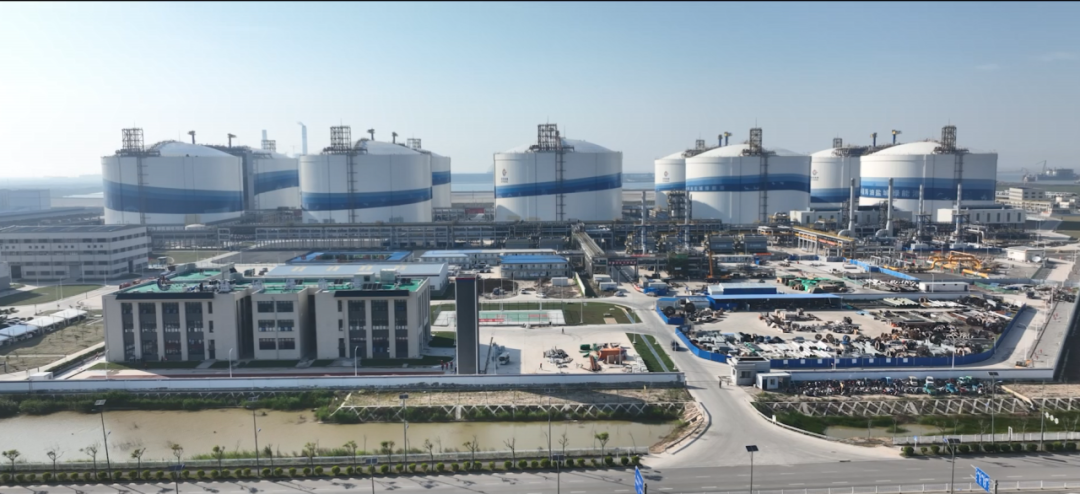
與22萬立方米LNG儲罐相比,27萬立方米LNG儲罐在儲存性能、經濟性等方面更具優勢。海油石化工程江蘇項目組負責鹽城“綠能港”一期擴建工程的設計、采辦、施工和試車。項目經理史厚增辦公室貼著的“綠能港”一期擴建工程藍圖上做滿了標記,紙邊因為磨損而微微卷起。
“建設首批27萬立方米LNG儲罐群,罐容的躍升對設計和建造提出了更高要求?!笔泛裨稣f,“我們憑借豐富的設計建造經驗,因地制宜推進中國海油CGTank大型LNG儲罐技術這一中國方案的工程轉化。”
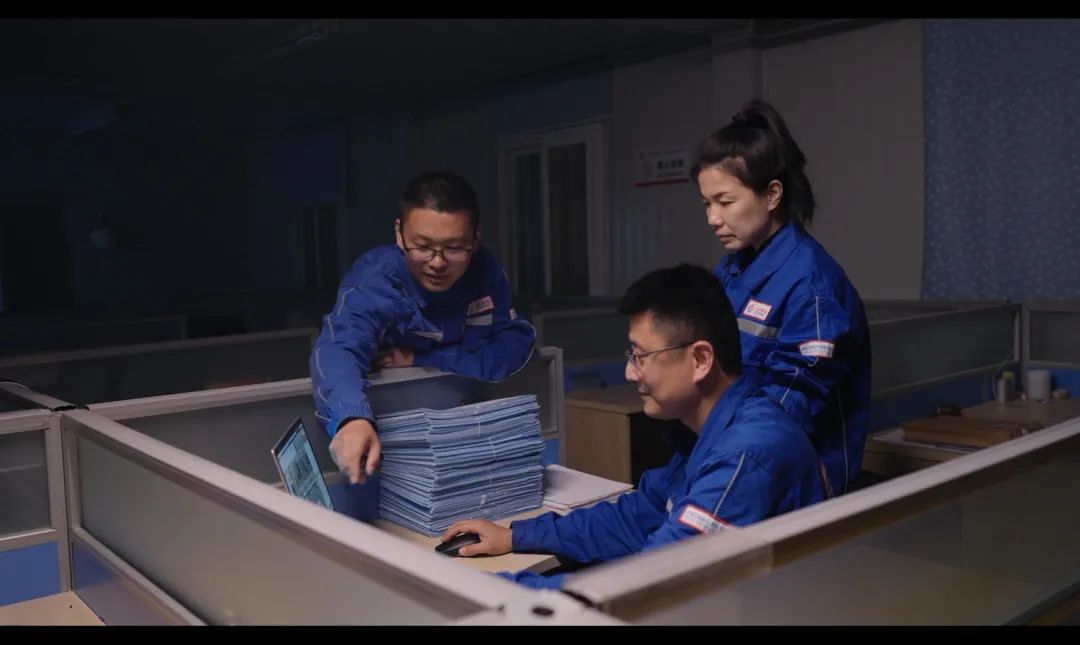
“我們將中國海油自主技術與建造實際相結合,進行工程化落地,因地制宜開展設計,”江蘇項目設計經理商麗娟說,“在現場安裝高峰期,設計團隊將與一期工程銜接最緊密的工藝廠區設計作為重點,集中力量攻關,設計代表常駐施工現場,隨時進行技術對接,根據現場情況調整設計參數,確保設計質量?!?/p>
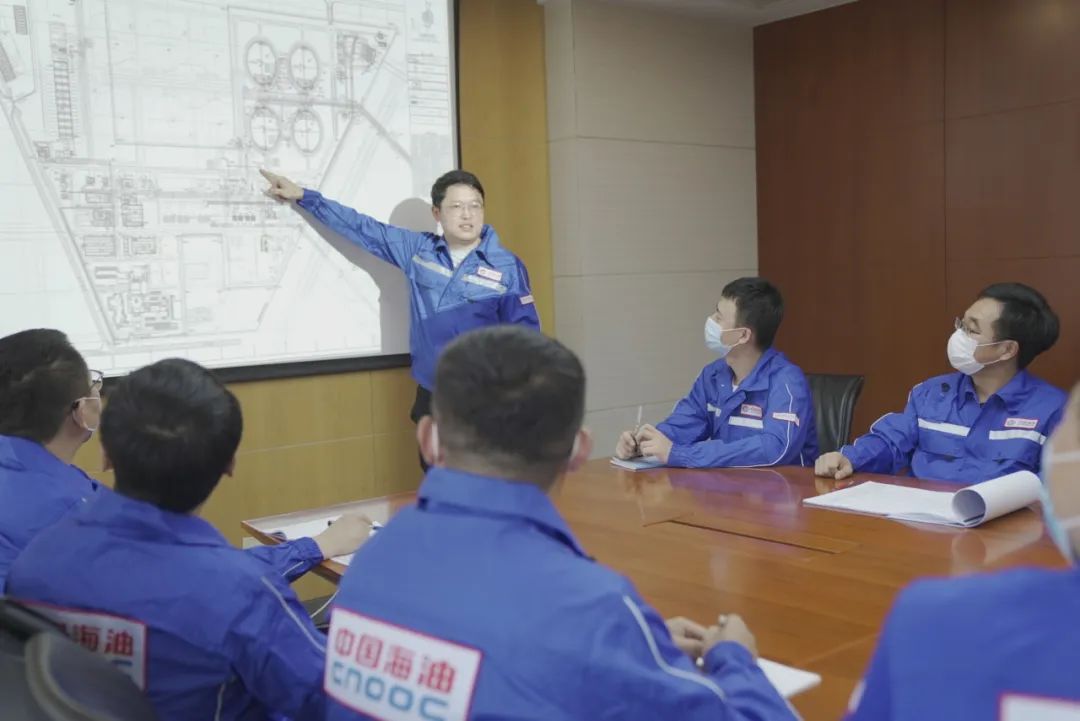
海油石化工程設計團隊采用數字化設計,繪就智慧藍圖。應用工程設計集成平臺,工藝、管道、設備等各專業實現線上聯動設計,整合設計過程數據,提高數據的準確性和完整性,提升設計效率。
實現全流程三維模型設計,立體展示儲罐和接收站設計布局,大到27萬立方米儲罐內外部細節,小到一個螺栓都能一目了然,更好地指導工程建設。
智慧建造
新技術新工藝打造優質工程
儲罐是液化天然氣產業鏈中的核心裝備,不僅存儲的介質溫度極低,為-162℃的液化天然氣,還需經受火災、爆炸、地震等極端工況考驗,對建造技術水平要求極高。鹽城“綠能港”項目建設過程中,創新采用新技術新工藝,用智慧建造打造優質工程。
鹽城“綠能港”項目所在地地處古黃河入??冢叵氯撬绍浀挠倌噘|黏土,單座罐體自身重量超過8萬噸,再加上儲罐里裝的是-162℃的液化天然氣,6座27萬立方米液化天然氣儲罐場地最大承重超過130萬噸,如何讓儲罐安穩立足?
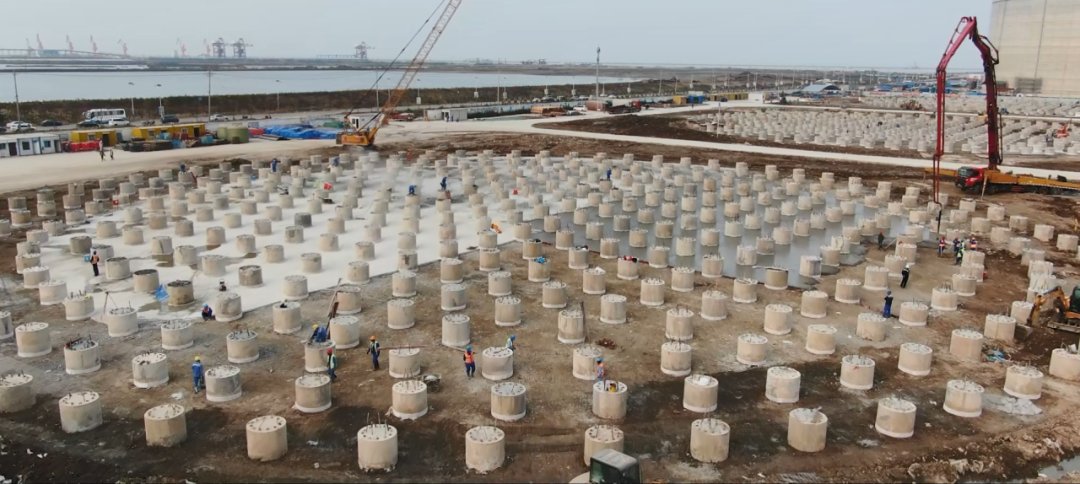
“每一座儲罐最下方由 406 根直徑1.5米、長75米的樁基牢牢撐起,”江蘇項目總工程師楊永剛說。項目首次采用一體化成樁技術,將75米長的樁基一次澆筑成型,采用“遠距離衛星定位沉樁定位系統”,智能化控制提升樁基施工精準度,用牢固的基座穩穩支撐儲罐。
儲罐內罐相當于保溫瓶的內膽,是保證液化天然氣儲罐低溫性能最重要的因素。27萬立方米液化天然氣儲罐內壁板高近45米,總重量近4000噸,焊接工作量大、技術要求高,安裝極具難度。
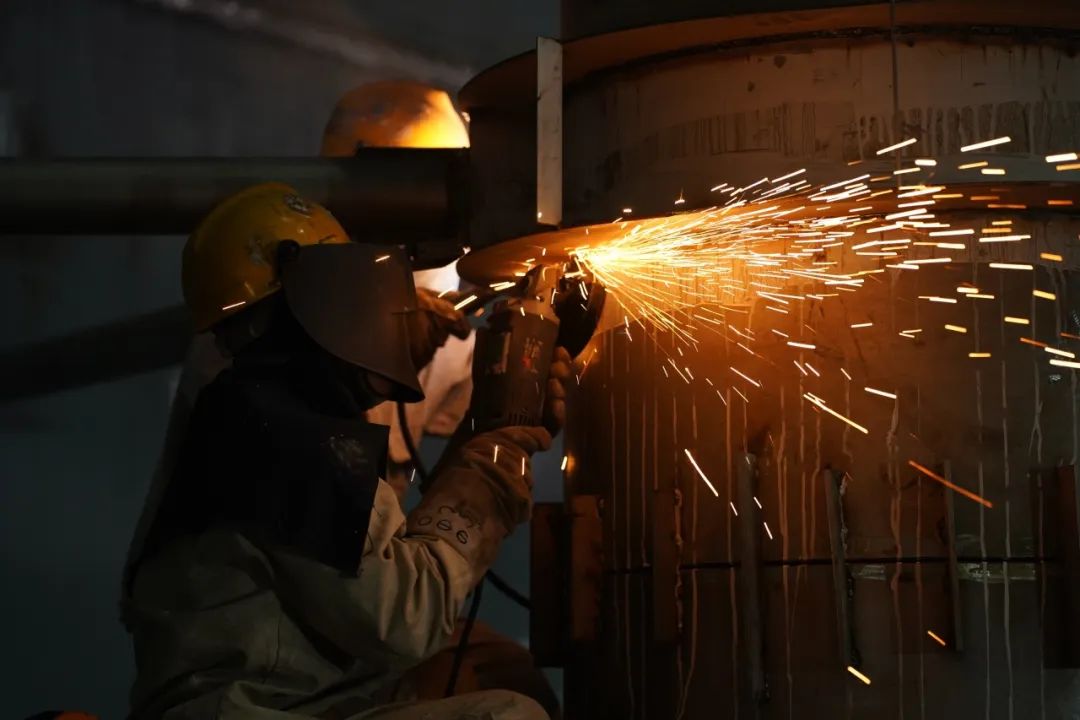
江蘇項目總工程師楊永剛說:“我們實行全過程監管,采用超聲波測厚儀、全站儀等精密檢測設備,逐張驗收、逐層檢測,將內罐壁板安裝主要參數的誤差成功控制在1毫米以內?!贝送猓€應用第四代焊接智能化檢測系統,采用AI智能閱片,提升了焊接進度和質量,6座儲罐內罐焊接一次合格率達99.51%,高于96%的行業一般水平。
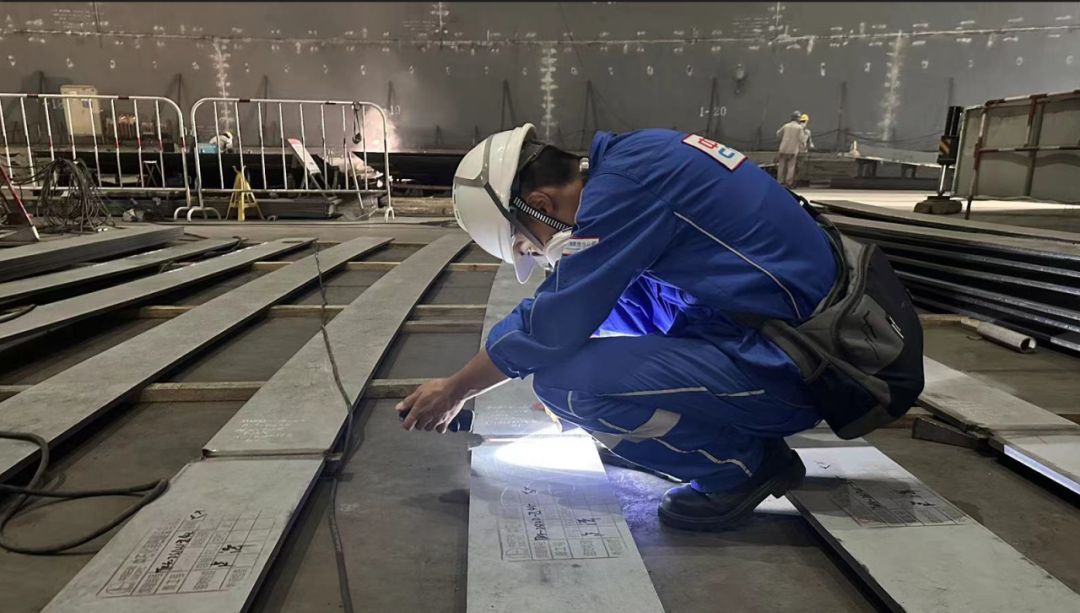
6座27萬方液化天然氣儲罐同時建設,工程量巨大,使用混凝土超過1056000立方米,鋼材超過93000噸,鋼材用量足夠建設2座鳥巢。在建設高峰期,施工現場有幾十個工種進行技術支持,共有18家主要施工單位,建設人員超過1860人。
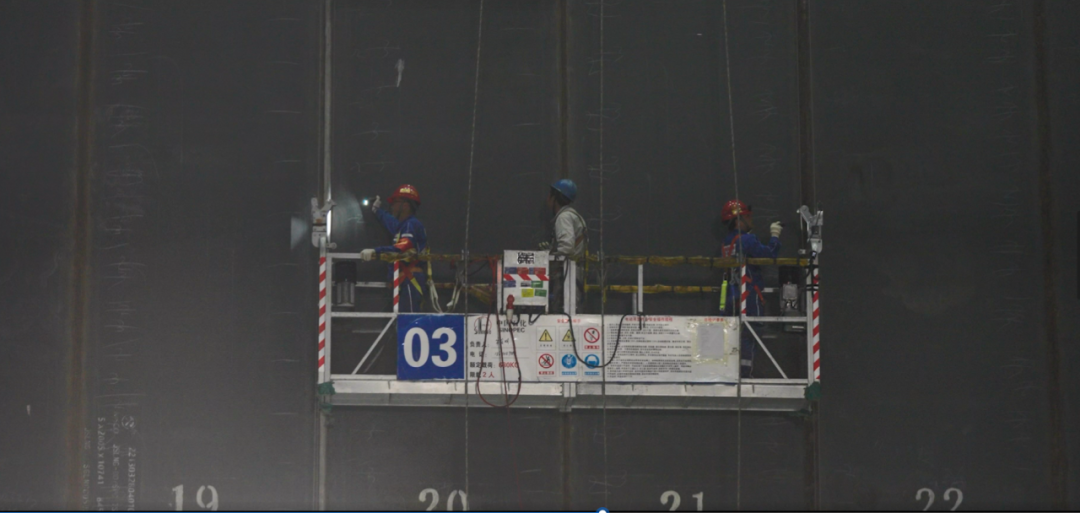
“我們用項目管理系統打通設計、采辦、施工全周期的標準化精細化管理,”海油石化工程副總經理張忠富說。江蘇項目組在項目現場打造“智慧工地”,全方位全時段掌握設備和人員工作狀態,施工作業全過程可追溯?!岸S碼干預”與“智慧工地”聯動,隱患排查“碼”上辦理,640多臺施工機具可視化動態管理。
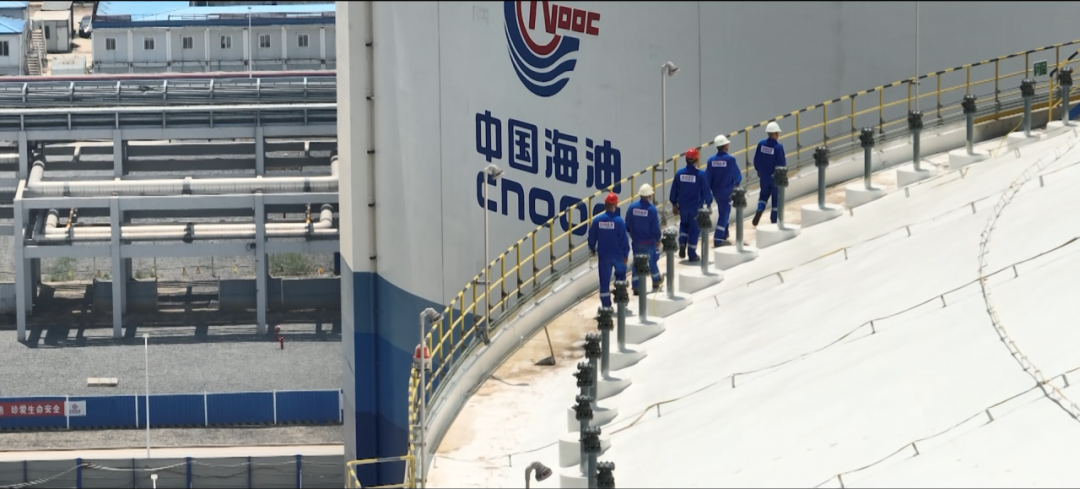
在高質量建設實體工程的同時,鹽城“綠能港”一期擴建工程以全專業數字化設計為起點,實施工程建設全過程數字化交付,為這一超級工程打造數字化“孿生兄弟”。
海油石化工程與合作單位一起,為鹽城“綠能港”打造了一個多維可視的數字化集成平臺,從設計采購到施工調試,項目全過程各階段產生的數據、文檔、模型都能通過平臺做到一目了然。同時,圍繞液化天然氣生產全鏈條管理的數智化轉型,重塑了生產流程,實現了能流監控與碳足跡的精細化管理,打造智慧“綠能港”。